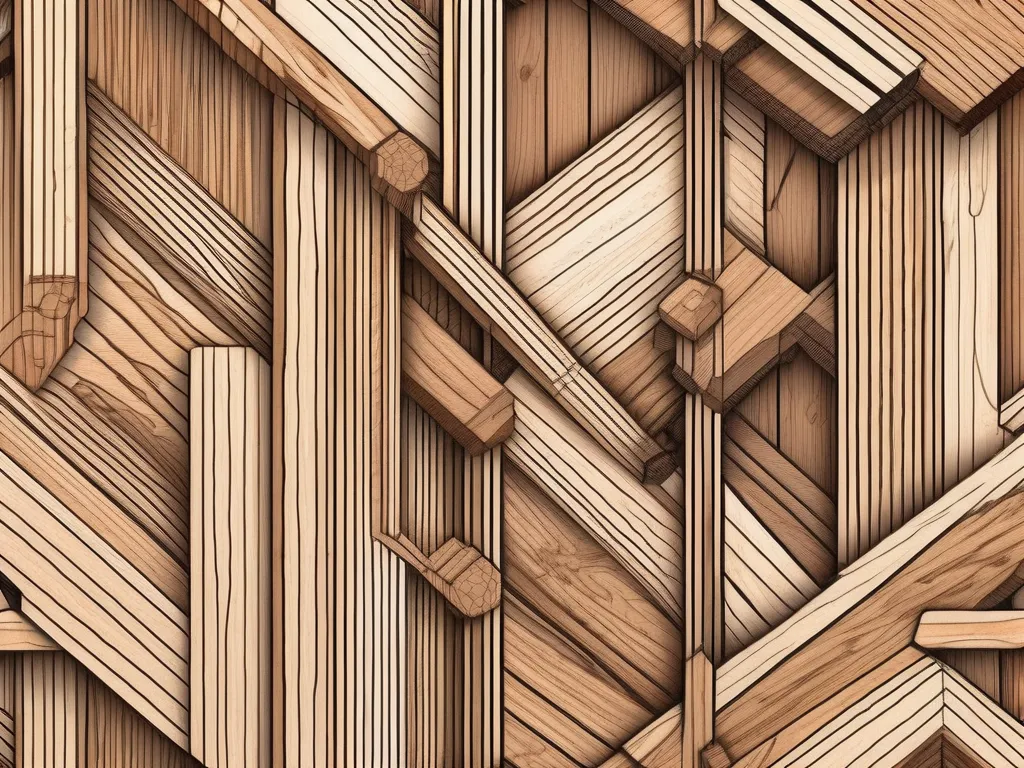
Japanese joinery is a traditional woodworking technique that has captivated people around the world with its intricate designs and seamless connections. One particular type of joinery that stands out is Hirakake-kakushi-meji-tsugi. In this article, we will delve into the art of Japanese joinery, explore the history and philosophy behind it, and understand the process of creating Hirakake-kakushi-meji-tsugi. We will also examine its role in modern architecture, the importance of preserving the tradition, and the future of Japanese joinery.
Understanding the Art of Japanese Joinery
The History and Evolution of Japanese Joinery
Japanese joinery dates back centuries, with its origins tracing back to the Asuka period (538-710 AD). Over time, Japanese craftsmen refined and developed their joinery techniques to create structures that could withstand the test of time. The evolution of joinery was heavily influenced by the available resources and the need to adapt to Japan's seismic activity.
During the Heian period (794-1185 AD), joinery techniques became more sophisticated as Buddhism spread throughout Japan. Temples and shrines required intricate joinery to showcase the craftsmanship and uphold their spiritual significance. Joinery became an art form, with each connection meticulously designed to enhance the overall structure.
One notable example of Japanese joinery during this period is the "yosegi-tsugi" technique, which involves interlocking pieces of wood to create a seamless and visually stunning joint. This technique was often used in the construction of temple roofs, where the precision of the joinery was essential to withstand the strong winds and heavy snowfall.
As Japan entered the Edo period (1603-1868 AD), joinery techniques continued to evolve. With the rise of the samurai class, the demand for fortified castles and residences grew. Joinery became a vital aspect of castle construction, with techniques like "tsugite" and "shiguchi" being employed to create strong connections that could withstand attacks and natural disasters.
During this period, joinery also found its way into everyday objects and furniture. The "sashimono" technique, for example, was used to create intricate wooden joints in cabinets and chests. These joints not only provided structural stability but also added an element of beauty to the furniture.
The Philosophy Behind Japanese Joinery
Japanese joinery is not simply about connecting two pieces of wood. It embodies a profound philosophy that embraces harmony, simplicity, and respect for nature. The philosophy of "Wabi-sabi" emphasizes the acceptance of imperfections and the beauty that comes from natural materials and aging.
The joinery itself reflects these principles, with designs that maximize the structural integrity without the need for nails or glue. Instead, the interlocking connections rely on precise cuts and friction to create strong and durable bonds. The result is a seamless integration of form and function, where each joint contributes to the overall aesthetic.
One example of this philosophy in practice is the "mortise and tenon" joint, known as "hozo" in Japanese. This joint involves a protruding piece of wood (tenon) fitting into a corresponding hole (mortise) to create a secure connection. The beauty of this joint lies in its simplicity and the way it allows the natural characteristics of the wood to shine through.
Another example is the "dovetail" joint, known as "kama-tsugi" in Japanese. This joint is often used in the construction of drawers and boxes, where its interlocking design provides both strength and visual appeal. The precision required to create a perfect dovetail joint is a testament to the skill and craftsmanship of Japanese joiners.
Japanese joinery is not just a technical skill; it is a way of life. It embodies a deep respect for nature and a commitment to creating structures that harmonize with their surroundings. From the intricate joinery of temples and shrines to the functional beauty of everyday objects, Japanese joinery continues to inspire awe and admiration around the world.
The Basics of Hirakake-kakushi-meji-tsugi
Hirakake-kakushi-meji-tsugi is a fascinating type of Japanese joinery that has been used for centuries to connect large horizontal beams to vertical support posts. Its primary purpose is to add stability and prevent the horizontal beam from sliding off the vertical post, ensuring the structural integrity of the overall construction.
The design of Hirakake-kakushi-meji-tsugi is a testament to the ingenuity and craftsmanship of Japanese joinery. It consists of a half-lap joint and a sliding dovetail joint, both of which work together to create a strong and secure connection. The half-lap joint allows for the horizontal beam to rest securely on the vertical post, while the sliding dovetail provides additional support by preventing any lateral movement.
When constructing Hirakake-kakushi-meji-tsugi, skilled craftsmen employ a variety of traditional tools that have been passed down through generations. These tools are essential for achieving the precision and accuracy required for this intricate joinery technique.
The Tools Required for Hirakake-kakushi-meji-tsugi
Creating Hirakake-kakushi-meji-tsugi requires the use of specific tools that have been honed and perfected over time. Among the traditional tools used are the Japanese saw, chisels of various sizes, a marking gauge, a mallet, and a plane.
The Japanese saw is a crucial tool in the process, as it allows craftsmen to make precise cuts with its fine teeth and flexible blade. The chisels, on the other hand, are used to remove excess material and create the necessary joints. Craftsmen carefully select chisels of different sizes to accommodate the varying needs of the joinery.
Accuracy is of utmost importance in Hirakake-kakushi-meji-tsugi, and that is where the marking gauge comes into play. This tool ensures that the measurements are precise, allowing for a perfect fit between the horizontal beam and the vertical post. The mallet is used to strike the chisels, providing the necessary force to remove the wood and shape the joints.
Lastly, the plane is employed to refine the surfaces of the wood, ensuring that they are smooth and even. This step is crucial for achieving a seamless connection between the horizontal beam and the vertical post, as any imperfections could compromise the stability and aesthetics of the joinery.
Overall, the construction of Hirakake-kakushi-meji-tsugi is a meticulous process that requires both skill and patience. From the careful measurements to the precise cuts and the refining of surfaces, every step is essential in creating a strong and visually pleasing connection between the horizontal beam and the vertical post.
The Process of Creating Hirakake-kakushi-meji-tsugi
Preparing the Wood for Joinery
Before beginning the joinery process, the wood must be carefully selected and prepared. In Japanese joinery, the choice of wood is crucial, as it affects both the durability and aesthetic of the final structure.
The wood is cut, dried, and seasoned to ensure stability and reduce the risk of warping. Each piece is then planed to create smooth surfaces and remove any imperfections that could hinder the joinery process. The craftsmen pay great attention to detail, as even the slightest deviation can affect the accuracy of the joints.
Once the wood is prepared, the craftsmen begin the intricate process of creating the Hirakake-kakushi-meji-tsugi joint. This joint is known for its strength and beauty, making it a popular choice in traditional Japanese woodworking.
Step-by-Step Guide to Hirakake-kakushi-meji-tsugi
The process of creating Hirakake-kakushi-meji-tsugi is intricate and requires precise measurements and cuts. Here is a step-by-step guide to help you understand the joinery process:
- Measure and mark the location of the joint on both the horizontal and vertical pieces of wood.
- Use a Japanese saw to make a vertical cut on the vertical post, creating a half-lap joint. This joint is created by removing half of the thickness of the wood from each piece, allowing them to interlock securely.
- Make a sliding dovetail joint on the horizontal beam, ensuring a perfect fit with the half-lap joint. The sliding dovetail joint is created by cutting a groove in the horizontal beam and a corresponding tongue on the vertical post. When the two pieces are fitted together, they create a strong and stable connection.
- Test the connection by sliding the horizontal beam onto the vertical post. The joint should be snug and secure, preventing any movement. This step is crucial to ensure the structural integrity of the joint.
- Fine-tune the joints using chisels, mallet, and plane to achieve a seamless connection. The craftsmen carefully remove any excess wood and make slight adjustments to ensure a perfect fit. This meticulous process requires skill and patience.
- Once the joints are finalized, the craftsmen apply a traditional Japanese wood finish to enhance the natural beauty of the wood and protect it from environmental factors. This finish not only adds a layer of protection but also brings out the unique grain patterns and colors of the wood.
Creating Hirakake-kakushi-meji-tsugi requires a deep understanding of woodworking techniques and a commitment to craftsmanship. The process is time-consuming and requires precision at every step. However, the end result is a stunning joint that showcases the skill and artistry of Japanese joinery.
The Role of Hirakake-kakushi-meji-tsugi in Modern Architecture
Hirakake-kakushi-meji-tsugi in Contemporary Japanese Buildings
While modern construction methods often rely on steel and concrete, there is still a place for traditional Japanese joinery in contemporary architecture. Architects and designers appreciate the aesthetic and structural qualities that Japanese joinery offers.
In Japan, you can find examples of Hirakake-kakushi-meji-tsugi in the construction of temples, traditional houses, and even modern public buildings. These structures showcase the timeless beauty of Japanese joinery and serve as a reminder of the deep-rooted craftsmanship that continues to flourish.
The Global Influence of Hirakake-kakushi-meji-tsugi
Japanese joinery, including Hirakake-kakushi-meji-tsugi, has gained international recognition and has influenced architecture and woodworking around the world. Architects and craftsmen from different cultures embrace the principles and techniques of Japanese joinery to create unique and sustainable structures.
The appreciation for the precision and versatility of Japanese joinery extends beyond functionality. It is seen as an art form that combines tradition, aesthetics, and functionality in perfect harmony.
Preserving the Tradition of Hirakake-kakushi-meji-tsugi
The Importance of Craftsmanship in Japanese Culture
In Japan, craftsmanship holds great importance. It is deeply ingrained in the culture and represents a connection to the past and the legacy of generations of skilled artisans. Preserving the tradition of Hirakake-kakushi-meji-tsugi ensures that this invaluable knowledge and skill continue to be passed down to future generations.
Craftsmanship is not limited to the act of creating functional objects but encompasses a way of life that values patience, attention to detail, and a deep understanding of the materials being used.
The Future of Hirakake-kakushi-meji-tsugi and Japanese Joinery
As the world continues to embrace sustainable and eco-friendly building practices, Japanese joinery, including Hirakake-kakushi-meji-tsugi, holds immense potential. Its construction techniques minimize waste and rely on natural materials, fostering a harmonious relationship between architecture and the environment.
The future of Hirakake-kakushi-meji-tsugi and Japanese joinery lies not only in its practical applications but also in its ability to inspire creativity and promote a deeper appreciation for craftsmanship worldwide.
In conclusion, Hirakake-kakushi-meji-tsugi represents the artistry, philosophy, and ingenuity of Japanese joinery. It is a testament to the craftsmanship and dedication of the craftsmen who have preserved this tradition for centuries. As we look to the future, we can draw inspiration from the past to create sustainable and beautiful structures that stand the test of time.
Inspired by the timeless beauty and sustainability of Hirakake-kakushi-meji-tsugi and traditional Japanese joinery, Quagga Designs brings the same ethos to modern living with our easy-to-assemble, MADE IN CANADA bed frames. Embracing the art of woodcraft, our No-Fuss Plus and Tic-Tac-Toe beds require no hardware for assembly, taking less time to set up than to unbox – typically less than 10 minutes. The No-Fuss Plus bed ingeniously expands to accommodate growing needs, from single to double and queen to king sizes, while the Accordion bed fits a range of mattress sizes. Our commitment to the environment is unwavering, with all-natural soy-based glue from Columbia Forest Products, FSC Certified Maple wood sourced from Quebec, and Mahogany that not only supports the local economy but also resonates with the quality used by renowned guitar makers. With no formaldehyde, Carb P2 compliance, and the ability to customize with any stain or paint, Quagga bed frames are the epitome of eco-friendly and versatile design. Plus, with features like increased weight capacity when slats are turned sideways and a 100-night sleep trial, we ensure your utmost satisfaction. We proudly support our community by partnering with charitable organizations and offer a 1-year warranty for peace of mind. Discover the most environmentally clean bed frames on the market and experience the fusion of tradition and innovation. Check out our products and join us in a journey of sustainable comfort and style.