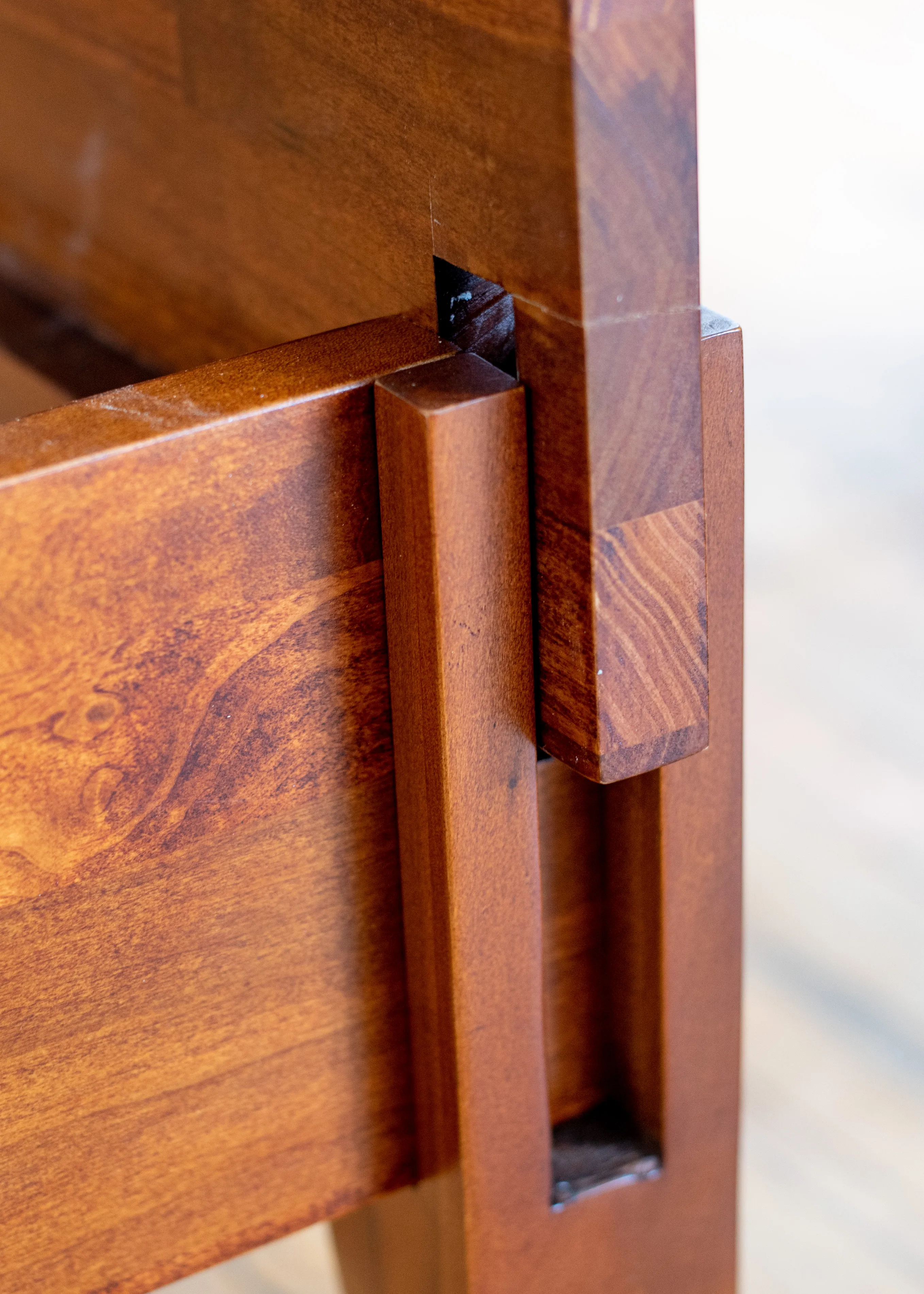
Japanese joinery is a centuries-old woodworking technique that is renowned for its precision, durability, and aesthetic appeal. Among the many styles of Japanese joinery, one of the most fascinating and intricate is Kinegata-chigiri-tsugi. In this article, we will explore the art of Japanese joinery and delve into the intricacies of Kinegata-chigiri-tsugi, its history, philosophy, techniques, applications, and future adaptations.
Understanding the Art of Japanese Joinery
Japanese joinery is rooted in a rich cultural tradition and reflects the Japanese philosophy of craftsmanship, known as "Kogei," which emphasizes the union of form and function. The art of Japanese joinery has evolved over centuries, influenced by various factors, including architecture, religion, and the availability of natural resources.
The intricate and precise craftsmanship of Japanese joinery is a testament to the dedication and skill of the craftsmen who have honed their techniques over generations. Each joint is carefully designed and executed to create a seamless connection between the different components of a structure. This attention to detail not only enhances the visual appeal of the finished piece but also ensures its durability and longevity.
One of the key aspects that sets Japanese joinery apart is its adaptability. The techniques have been refined and adapted to suit different architectural styles and purposes. From the elegant simplicity of a traditional tea house to the grandeur of a temple or castle, Japanese joinery techniques have been utilized to create a wide range of structures that are both functional and aesthetically pleasing.
The History and Evolution of Japanese Joinery
The history of Japanese joinery can be traced back to the Asuka period (538-710 CE) when Japan started importing Buddhist architecture and carpentry techniques from China and Korea. Over time, these techniques were adapted and evolved to suit the unique needs and preferences of the Japanese people.
During the Heian period (794-1185 CE), Japanese architecture flourished, and joinery techniques became more refined and intricate. The development of the Japanese tea ceremony and the construction of tea houses further fueled the advancement of joinery, as intricate details and precise craftsmanship were essential in creating tranquil and harmonious spaces.
From the Kamakura period (1185-1333 CE) to the Edo period (1603-1868 CE), Japanese joinery techniques continued to evolve and flourish. The construction of temples, shrines, and castles necessitated the creation of intricate joints that could withstand earthquakes and other natural forces. During this period, master craftsmen perfected their skills, passing down their knowledge through apprenticeships.
One of the most famous examples of Japanese joinery is found in the construction of Horyuji Temple in Nara, which dates back to the 7th century. The temple showcases the sophisticated joinery techniques that were employed to create a structure that has withstood the test of time.
The Philosophy Behind Japanese Joinery
Japanese joinery is not merely a technical skill but is deeply rooted in the philosophy of harmony, simplicity, and respect for nature. The Japanese concept of "wa" or harmony extends to every aspect of Japanese life, including architecture and craftsmanship. Joinery seeks to create a harmonious relationship between materials, structures, and the surrounding environment.
Another fundamental principle of Japanese joinery is the idea of "Mottainai," which translates to "waste nothing." This concept emphasizes the efficient use of resources, promoting sustainability and minimizing waste. Japanese joinery techniques often maximize the strength and stability of the wood, reducing the need for additional hardware or adhesives.
Furthermore, Japanese joinery is deeply influenced by the concept of "Ma," which refers to the space between objects. This notion of negative space is considered just as important as the physical elements themselves, creating a sense of balance and tranquility in the overall design.
Throughout history, Japanese joinery has not only served functional purposes but also played a significant role in the artistic expression of Japanese culture. The intricate joints and elegant designs are a testament to the craftsmanship and creativity of the Japanese people, showcasing their ability to transform wood into works of art.
The Basics of Kinegata-chigiri-tsugi
Among the diverse array of joints used in Japanese joinery, Kinegata-chigiri-tsugi stands out for its unique characteristics and aesthetic appeal. This joint, often referred to as the "pinwheel joint," is a complex interlocking joint commonly used in the construction of traditional Japanese rooms, furniture, and tea houses.
The art of Japanese joinery has a long and rich history, dating back centuries. It is a testament to the skill and craftsmanship of Japanese carpenters, who have perfected the art of creating intricate and beautiful joints that not only serve a functional purpose but also elevate the overall design of a structure.
Kinegata-chigiri-tsugi is a prime example of this craftsmanship. It is a joint that not only connects two pieces of wood but also adds a touch of elegance and sophistication to the finished product. The intricate "pinwheel" pattern created by this joint is a visual delight, capturing the attention of anyone who sees it.
The Unique Characteristics of Kinegata-chigiri-tsugi
Kinegata-chigiri-tsugi is characterized by its intricate "pinwheel" pattern, achieved through a series of overlapping and interlocking components. This joint not only enhances the structural integrity of the connected pieces but also creates an attractive visual motif that adds to the overall beauty of the finished structure.
When observing a structure that incorporates Kinegata-chigiri-tsugi, one cannot help but marvel at the precision and skill required to create such a joint. Each component is meticulously crafted to fit seamlessly with the others, resulting in a joint that is not only strong but also visually stunning.
Furthermore, the pinwheel pattern created by this joint adds a sense of movement and dynamism to the overall design. It is as if the joint itself is alive, with each component working in harmony to create a cohesive and captivating whole.
One of the key features of Kinegata-chigiri-tsugi is its ability to create a seamless connection without the need for nails or adhesives. The joint's components fit together meticulously, ensuring a tight and secure fit. The precision and stability of this joint make it suitable for withstanding the rigors of earthquakes, which are common in Japan.
It is fascinating to consider the engineering principles behind Kinegata-chigiri-tsugi. The interlocking components distribute the weight and forces applied to the joint evenly, minimizing stress concentration and increasing the joint's overall strength. This is a testament to the ingenuity and knowledge of Japanese carpenters, who have developed sophisticated techniques to create joints that can withstand the test of time.
The Tools and Materials Used in Kinegata-chigiri-tsugi
Creating a Kinegata-chigiri-tsugi joint requires the skillful use of traditional Japanese hand tools, such as chisels, saws, and planes. These tools, often handmade by expert craftsmen, are specifically designed to ensure precision and accuracy in the creation of intricate joints.
The process of creating a Kinegata-chigiri-tsugi joint is a labor-intensive one, requiring patience, skill, and attention to detail. The carpenter must carefully measure and mark the wood, ensuring that each component is cut to the exact specifications required for a perfect fit.
The primary material used in Kinegata-chigiri-tsugi is wood, specifically high-quality hardwoods such as Japanese cypress (hinoki), Japanese cedar (sugi), and Japanese oak (kashi). These woods are prized for their durability, natural beauty, and resistance to rot and decay.
Japanese carpenters have a deep respect for the materials they work with, often selecting wood that has been carefully aged and dried to ensure stability and longevity. The choice of wood is crucial in creating a joint that not only functions flawlessly but also ages gracefully, developing a rich patina over time.
It is worth noting that the selection of wood for a Kinegata-chigiri-tsugi joint is not solely based on its physical properties. Japanese carpenters also consider the symbolic meaning associated with different types of wood. For example, hinoki is often used in the construction of sacred spaces and tea houses due to its association with purity and tranquility.
In conclusion, Kinegata-chigiri-tsugi is a remarkable joint that showcases the skill and artistry of Japanese carpenters. Its unique characteristics and aesthetic appeal make it a sought-after technique in traditional Japanese construction. The precision, stability, and visual beauty of this joint are a testament to the mastery of Japanese joinery, an art form that continues to inspire and captivate people around the world.
The Process of Kinegata-chigiri-tsugi
The process of creating a Kinegata-chigiri-tsugi joint involves several meticulous steps, each requiring precision and mastery of the craft. From selecting the appropriate wood to finishing the joint, each stage demands careful attention to detail and a deep understanding of the materials and techniques involved.
Preparing the Wood for Kinegata-chigiri-tsugi
Prior to creating a Kinegata-chigiri-tsugi joint, the wood must be carefully selected and prepared. The wood is typically dried and aged to ensure stability and eliminate moisture content that could lead to warping or shrinking. The surface of the wood is then meticulously planed and smoothed, ready for the intricate joint cutting process.
The Step-by-Step Procedure of Kinegata-chigiri-tsugi
The creation of a Kinegata-chigiri-tsugi joint involves a series of precise cuts, notches, and interlocking components. The joint is carefully laid out and marked on the wood, ensuring accurate positioning and alignment. Skilled craftsmen then use a combination of traditional hand tools to cut and shape the components, allowing them to fit together seamlessly.
During this process, the accuracy and precision of each cut are of utmost importance. Any deviation can compromise the integrity of the joint and affect the overall strength and stability of the finished structure. Consequently, years of experience and a deep understanding of the craft are necessary to achieve mastery in creating Kinegata-chigiri-tsugi joints.
The Applications of Kinegata-chigiri-tsugi
Kinegata-chigiri-tsugi finds a wide range of applications in traditional Japanese craftsmanship, particularly in furniture making and architecture. The joint's intricate design and superior strength make it ideal for creating elegant and long-lasting wooden structures.
Kinegata-chigiri-tsugi in Furniture Making
In furniture making, Kinegata-chigiri-tsugi is often used to create joints between structural components, such as corner supports and legs, ensuring the stability and durability of the furniture. This joint adds a touch of sophistication to wooden furniture, elevating its aesthetic appeal while maintaining its functionality.
Kinegata-chigiri-tsugi in Architecture
Kinegata-chigiri-tsugi has been widely employed in traditional Japanese architecture, particularly in the construction of tea houses and other ceremonial structures. The joint's ability to withstand strong forces and its intricate design contribute to the overall beauty and structural integrity of these buildings, creating spaces that evoke a sense of tranquility and harmony.
The Future of Kinegata-chigiri-tsugi
While Kinegata-chigiri-tsugi is deeply rooted in tradition, it continues to evolve and adapt to the changing needs and preferences of modern society. With advancements in technology and the emergence of new materials, contemporary craftsmen have embraced the challenge of preserving the essence of Kinegata-chigiri-tsugi while exploring new possibilities.
Modern Adaptations of Kinegata-chigiri-tsugi
In recent years, innovative craftsmen have incorporated Kinegata-chigiri-tsugi into modern furniture and architectural designs, blending tradition with contemporary aesthetics. This fusion of styles not only preserves the essence of Japanese joinery but also showcases its timeless beauty in a modern context, appealing to a wider audience.
Preserving the Tradition of Kinegata-chigiri-tsugi
Despite the allure of modern adaptations, there is a dedicated effort to preserve the traditional techniques and knowledge associated with Kinegata-chigiri-tsugi. Organizations, such as the Traditional Japanese Crafts Association, collaborate with master craftsmen to ensure the transmission of skills and encourage the appreciation of traditional joinery techniques.
In conclusion, Kinegata-chigiri-tsugi is a unique and captivating style of Japanese joinery that exemplifies the country's rich cultural heritage and craftsmanship. With its intricate designs, meticulous construction, and inherent strength, Kinegata-chigiri-tsugi continues to inspire admiration and fascination in contemporary society. Whether it is used in traditional furniture or modern architectural applications, this remarkable joint serves as a testament to the enduring beauty and functionality of Japanese joinery.
Inspired by the timeless beauty and functionality of Kinegata-chigiri-tsugi, Quagga Designs brings the elegance of Japanese joinery to your bedroom with our easy-to-assemble, MADE IN CANADA bed frames. Embracing the same principles of harmony and sustainability, our No-Fuss Plus and Tic-Tac-Toe beds require no hardware, assembling in less than 10 minutes—often taking more time to unbox than to put together. The No-Fuss Plus bed ingeniously expands to accommodate growing space needs, transitioning from single to double and queen to king sizes, while the Accordion bed fits a range of mattress sizes. Our commitment to the environment is reflected in the use of all-natural soy-based glue from Columbia Forest Products and the sourcing of FSC Certified Maple wood from Quebec and Mahogany from Africa, ensuring no formaldehyde is present in any of our products. Not only do Quagga bed frames support our local economy and reduce landfill waste, but they also offer unparalleled customization, allowing you to apply any stain or paint to match your decor. With a 1-year warranty, a 100-night sleep trial, and partnerships with charitable organizations, Quagga Designs stands at the forefront of eco-friendly and socially responsible furniture. Experience the most environmentally clean bed frames on the market today, with shipping available throughout Canada and the continental United States. Check out our products and bring a piece of artisanal craftsmanship into your home.