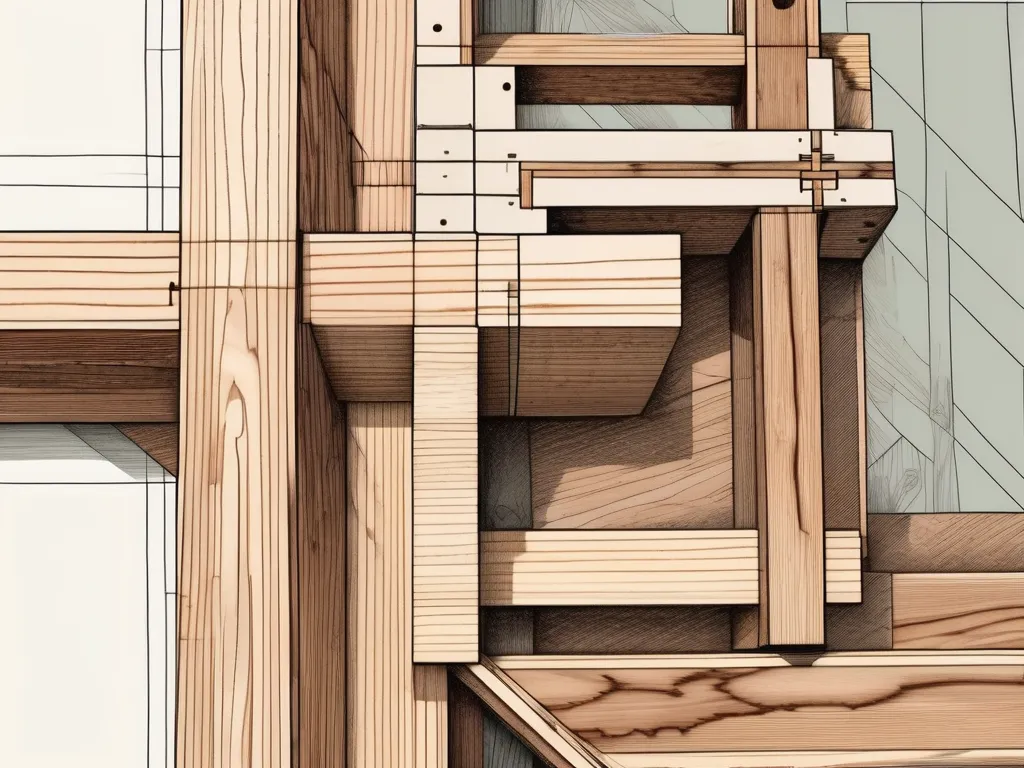
Japanese joinery is a traditional woodworking technique that has captivated craftsmen and admirers around the world. Among the various forms of joinery, Okkake-daisen-tsugi stands out for its unique structural and aesthetic qualities. In this article, we will delve into the intricacies of Okkake-daisen-tsugi, exploring its history, philosophy, and applications in Japanese architecture. We will also examine the process of creating this exquisite joint and discuss its future in the world of woodworking.
Understanding the Art of Japanese Joinery
Japanese joinery is founded upon centuries of craftsmanship and a deep respect for wood as a living material. It combines precise measurements, intricate cuts, and friction-fit connections to create strong and visually appealing structures. The artistry behind Japanese joinery lies in its ability to create functional joints that are also true works of art.
When observing a piece of Japanese joinery, one cannot help but be captivated by the level of detail and precision that goes into each joint. Every cut is made with intention, and every connection is carefully crafted to ensure a seamless fit. It is a testament to the skill and dedication of the craftsmen who have honed their craft over generations.
The History of Japanese Joinery
Japanese joinery has a rich history that can be traced back to the Asuka period (592-710). During this time, Buddhism was introduced to Japan, bringing with it advanced architectural techniques from China and the Korean peninsula. These techniques were melded with indigenous woodworking traditions, giving birth to the distinctive style of Japanese joinery that we know today.
As the centuries passed, Japanese joinery continued to evolve and diversify. Different regions developed their own unique styles and techniques, each with its own distinct characteristics. From the intricate puzzle-like joints of the Edo period to the elegant simplicity of the Sukiya-zukuri style, Japanese joinery became an integral part of the country's architectural heritage.
One of the remarkable aspects of Japanese joinery is its ability to withstand the test of time. Many ancient wooden structures, such as temples and shrines, have survived for centuries, thanks to the durability and strength of the joinery techniques used. This is a testament to the ingenuity and engineering prowess of the craftsmen who mastered the art of Japanese joinery.
The Philosophy Behind Japanese Joinery
Japanese joinery goes beyond mere functionality; it embodies a philosophical approach that emphasizes harmony, simplicity, and sustainability. It reflects the belief that architecture should be in harmony with nature and that every joint should be crafted with utmost care and respect for the wood.
Central to the philosophy of Japanese joinery is the concept of "Ma," which refers to the space between objects. It is the understanding that the negative space is just as important as the physical elements themselves. Japanese joinery seeks to create a sense of balance and tranquility by carefully considering the relationship between the joints and the spaces they create.
This philosophy is rooted in the Japanese aesthetic concept of wabi-sabi, which celebrates imperfections and the beauty of natural materials. The joinery is designed to highlight the unique characteristics of the wood, such as its grain pattern and color variations, rather than concealing them. This approach not only enhances the visual appeal of the structure but also allows the wood to age gracefully, developing a patina that tells the story of its journey through time.
Japanese joinery is not just a technical skill; it is an art form that embodies the spirit of craftsmanship and the deep connection between humans and nature. It is a testament to the ingenuity and creativity of the Japanese people, who have transformed a practical necessity into a true expression of beauty and harmony.
The Basics of Okkake-daisen-tsugi
Okkake-daisen-tsugi is a specific type of Japanese joinery that is characterized by its interlocking design. It is commonly used to create strong connections between structural elements in traditional Japanese buildings, such as beams, posts, and lintels.
Traditional Japanese architecture is known for its intricate joinery techniques, and Okkake-daisen-tsugi is no exception. This particular joint is revered for its strength and durability, making it an essential component in the construction of buildings that can withstand the test of time.
The design of Okkake-daisen-tsugi is based on a series of tenons and mortises that interlock with one another. The joints are carefully fitted and secured with friction, without the need for nails or adhesives. This design not only ensures structural stability but also allows for easy disassembly and reassembly if necessary.
When constructing a building using Okkake-daisen-tsugi, the craftsmen meticulously measure and cut each piece of wood to ensure a perfect fit. The precision required in creating these joints is a testament to the skill and expertise of the artisans who practice this traditional craft.
The Design of Okkake-daisen-tsugi
The design of Okkake-daisen-tsugi is a marvel of engineering and craftsmanship. Each joint is carefully planned and executed to create a seamless connection between the structural elements of a building. The interlocking tenons and mortises provide a strong and secure bond that can withstand the forces of nature, including earthquakes and strong winds.
One of the key features of Okkake-daisen-tsugi is its ability to distribute weight evenly across the joint. This design ensures that the load-bearing capacity of the joint is maximized, making it ideal for supporting heavy structural elements. The interlocking nature of the joint also helps to prevent any movement or shifting, further enhancing its stability.
Another advantage of Okkake-daisen-tsugi is its aesthetic appeal. The clean lines and precise fit of the joint create a visually pleasing effect, adding to the overall beauty of traditional Japanese architecture. The craftsmanship involved in creating these joints is highly regarded, and the joint itself is often considered a work of art.
The Tools Required for Okkake-daisen-tsugi
Creating Okkake-daisen-tsugi requires a range of traditional woodworking tools, including chisels, saws, and mallets. These tools are used to make precise cuts, carve out mortises, and shape the tenons. The craftsmanship and skill involved in using these tools contribute to the artistry of the joint.
Chisels are essential for creating the mortises, which are the recessed slots that receive the tenons. The craftsmen carefully carve out these slots, ensuring a tight fit between the two pieces of wood. Sawing techniques are employed to shape the tenons, creating the interlocking elements of the joint.
The mallet is used to gently tap the pieces of wood together, securing the joint through friction. This process requires finesse and precision, as too much force can damage the joint, while too little force may result in a loose connection. The craftsmen rely on their experience and expertise to strike the perfect balance.
Overall, the tools used in creating Okkake-daisen-tsugi are an extension of the artisan's skill and dedication. Each tool is carefully selected and maintained to ensure the highest level of craftsmanship. The combination of these tools and the traditional techniques passed down through generations result in the creation of exquisite joinery that is both functional and visually stunning.
The Process of Creating Okkake-daisen-tsugi
The creation of Okkake-daisen-tsugi involves a series of meticulous steps, each essential in achieving a structurally sound and visually pleasing joint.
Okkake-daisen-tsugi, also known as the sliding dovetail joint, is a traditional Japanese woodworking technique that has been perfected over centuries. This joint is not only functional but also adds an aesthetic appeal to the overall design of the piece.
Preparing the Wood
Before the construction of Okkake-daisen-tsugi can begin, the wood must be carefully selected and prepared. The wood must be seasoned, eliminating excess moisture to prevent warping or shrinking once the joint is assembled.
Traditional Japanese woodworkers often use hand tools, such as planes and scrapers, to create a smooth and even surface on the wood. This meticulous preparation ensures that the joint fits together seamlessly.
Furthermore, the selection of wood is crucial to the success of the joint. Different types of wood have varying characteristics, such as hardness and grain pattern, which can affect the strength and visual appeal of the joint. Experienced woodworkers take these factors into consideration when choosing the perfect piece of wood for Okkake-daisen-tsugi.
Cutting Techniques
One of the distinguishing features of Okkake-daisen-tsugi is its intricate cutting techniques. These techniques require precise measurements and steady hands to create the interlocking tenons and mortises that form the joint.
Woodworkers employ a combination of saws, chisels, and other cutting tools to shape the tenons and mortises. Each cut must be made with utmost care to achieve a perfect fit and ensure the stability of the joint.
Furthermore, the angle and depth of the cuts play a crucial role in the overall strength and durability of the joint. Woodworkers carefully calculate these measurements to ensure that the joint will withstand the test of time.
Assembling the Joint
Once the wood has been prepared and the tenons and mortises cut, it is time to assemble the Okkake-daisen-tsugi joint. The tenons are carefully inserted into the corresponding mortises, and the joint is then secured with a friction-fit connection.
Woodworkers often use wooden mallets to gently tap the joint into place, ensuring a tight fit. The precision and skill required to assemble the joint without damaging the wood is a testament to the mastery of Japanese joinery.
After the joint is assembled, any excess material is carefully removed, and the joint is sanded to create a smooth and seamless finish. This attention to detail ensures that the joint not only functions flawlessly but also adds a touch of elegance to the overall piece.
Okkake-daisen-tsugi is a testament to the craftsmanship and dedication of traditional Japanese woodworking. The process of creating this joint requires patience, precision, and a deep understanding of the characteristics of wood. The end result is a joint that not only connects two pieces of wood but also showcases the beauty and artistry of Japanese joinery.
The Role of Okkake-daisen-tsugi in Japanese Architecture
Okkake-daisen-tsugi plays a crucial role in traditional Japanese architecture and is found in various types of buildings across the country.
Traditional Japanese Buildings and Okkake-daisen-tsugi
Traditional Japanese buildings, such as temples, shrines, and tea houses, often feature Okkake-daisen-tsugi joints. These joints not only provide structural stability but also contribute to the distinctive aesthetic of these buildings.
Okkake-daisen-tsugi often includes elaborate decorative elements, such as carved patterns and intricate designs, adding a touch of artistry to the structure.
Modern Applications of Okkake-daisen-tsugi
While Okkake-daisen-tsugi is deeply rooted in tradition, it continues to find relevance in modern architecture. Contemporary designers and architects are exploring ways to incorporate this traditional joint into contemporary structures, infusing them with a sense of history and craftsmanship.
Okkake-daisen-tsugi has also found applications beyond Japan's borders, as woodworking enthusiasts and craftsmen worldwide appreciate its beauty and structural integrity.
The Future of Okkake-daisen-tsugi
The art of Okkake-daisen-tsugi is not stagnant; it continues to evolve and adapt to the changing times.
Innovations in Japanese Joinery
With advancements in technology and design, innovations in Japanese joinery, including Okkake-daisen-tsugi, are emerging. Woodworkers and designers are experimenting with new techniques and materials to push the boundaries of what is possible with this ancient craft.
Preserving the Art of Okkake-daisen-tsugi
As modern construction techniques and materials become prevalent, the traditional art of Okkake-daisen-tsugi faces the risk of being forgotten. However, dedicated craftsmen and organizations are working tirelessly to preserve and promote this unique form of joinery.
Efforts are being made to pass on the knowledge and skills of Okkake-daisen-tsugi to future generations through apprenticeships, workshops, and educational programs. By valuing and cherishing this ancient art form, we ensure that Okkake-daisen-tsugi will continue to inspire and captivate woodworking enthusiasts for years to come.
In conclusion, Okkake-daisen-tsugi represents the essence of Japanese joinery—a harmonious blend of craftsmanship, philosophy, and artistry. Its history, design, and applications in Japanese architecture all contribute to its enduring appeal. As we look to the future, it is reassuring to know that the legacy of Okkake-daisen-tsugi will continue to thrive and inspire new generations of woodworkers around the world.
Inspired by the timeless beauty and precision of Okkake-daisen-tsugi, Quagga Designs brings the same dedication to craftsmanship and sustainability to your bedroom. Our easy-to-assemble bed frames, made in Canada, embody the spirit of traditional joinery with modern innovation. With no hardware needed for our No-Fuss Plus and Tic-Tac-Toe beds, you'll spend more time enjoying the simplicity of design than assembling it—taking less than 10 minutes to set up. The No-Fuss Plus bed ingeniously expands to accommodate growing space needs, while the Accordion bed caters to a range of sizes from single xl to king. We are committed to environmental responsibility, using all-natural soy-based glue and sourcing FSC Certified Maple wood from Quebec and Mahogany for our No-Fuss Plus bed, recognized for its rich tone by leading guitar manufacturers like Fender. Our bed frames are free of formaldehyde, Carb P2 compliant, and customizable to your aesthetic preferences. Proudly made in Canada, our products support the local economy and are shipped throughout Canada and the continental United States. Designed for durability, our bed frames can increase weight capacity fivefold by simply turning the slats sideways. In partnership with charitable organizations and offering a 1-year warranty, Quagga Designs is dedicated to quality and community. Experience our commitment to excellence with a 100-night sleep trial. Embrace the harmony of Japanese joinery and modern functionality with Quagga Designs, where beauty and sustainability meet practicality. Check out our products and transform your sleep space today.