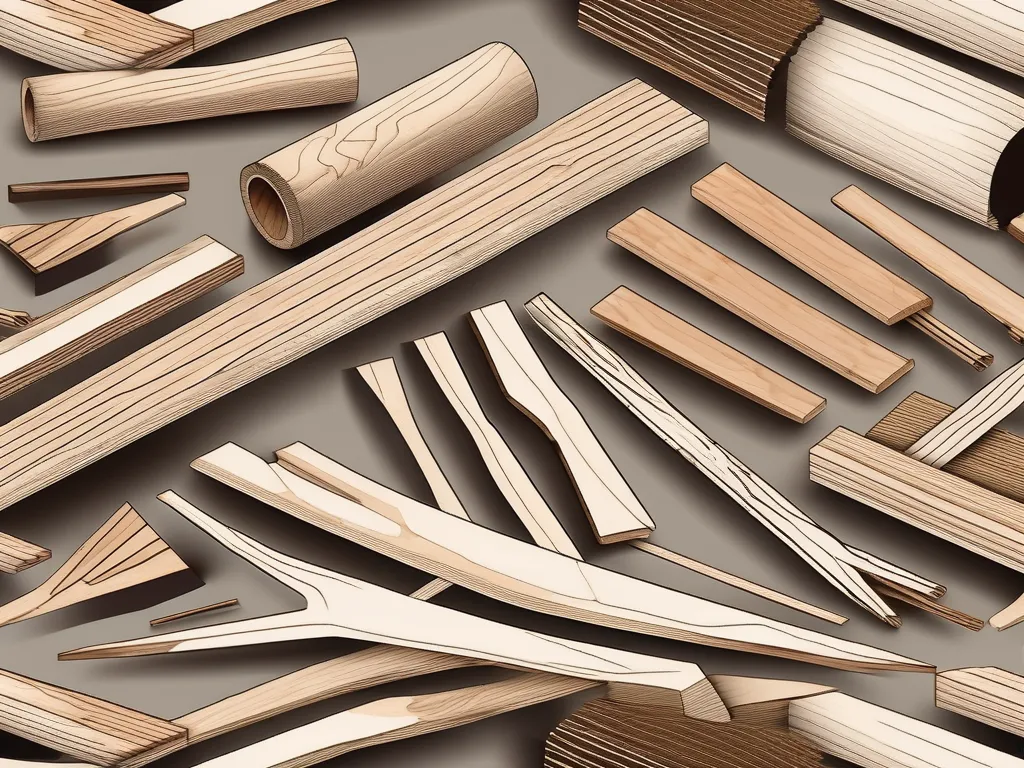
Sao-shachi-tsugi is a traditional Japanese joinery technique that has been used for centuries in the construction of wooden structures. This intricate and precise method involves the interlocking of wooden beams and columns without the use of nails or screws. In this article, we will delve into the world of Sao-shachi-tsugi, exploring its history, philosophy, art, technique, role in Japanese architecture, and its importance in preserving the rich tradition of Japanese craftsmanship.
Understanding Sao-shachi-tsugi
Sao-shachi-tsugi is more than just a method of joinery; it embodies the essence of Japanese craftsmanship and is a testament to the meticulous attention to detail that characterizes traditional Japanese carpentry. To truly understand the technique, it is essential to delve into its history and philosophy.
The History of Sao-shachi-tsugi
The origins of Sao-shachi-tsugi can be traced back to ancient Japan, where it was developed by skilled carpenters who sought to create structures that could withstand earthquakes and other natural disasters. These carpenters were inspired by the need to build resilient and durable buildings that could withstand the unpredictable forces of nature.
The technique of Sao-shachi-tsugi was refined over centuries, as carpenters experimented with different methods of joinery and construction. They observed the effects of earthquakes and used that knowledge to improve their techniques, making them more effective at creating stable and long-lasting structures.
As the technique gained popularity, it became an integral part of Japanese architecture. From humble homes to grand temples, Sao-shachi-tsugi was used to create buildings that were not only functional but also aesthetically pleasing.
The Philosophy Behind Sao-shachi-tsugi
At the heart of Sao-shachi-tsugi lies the philosophy of harmony and balance. Japanese carpenters believe that the natural beauty of the wood should not be compromised by the use of metal fasteners, and that the joinery itself should enhance the overall aesthetics of the structure.
When crafting a Sao-shachi-tsugi joint, carpenters pay close attention to the grain and texture of the wood. They carefully select pieces that complement each other, ensuring that the joint seamlessly blends into the overall design. This attention to detail is what sets Sao-shachi-tsugi apart from other joinery techniques.
In addition to its aesthetic value, Sao-shachi-tsugi is also known for its structural integrity. The interlocking nature of the joints creates a strong and stable connection, allowing the wood to expand and contract with changes in temperature and humidity without compromising the overall stability of the structure.
Furthermore, the philosophy behind Sao-shachi-tsugi extends beyond the physical aspects of carpentry. It reflects a deep respect for nature and a desire to work in harmony with the environment. By using natural materials and traditional techniques, Japanese carpenters strive to create buildings that are in harmony with their surroundings.
Overall, Sao-shachi-tsugi is not just a technique; it is a reflection of the rich history and philosophy of Japanese carpentry. It represents the dedication and skill of craftsmen who have honed their craft over generations, creating structures that are not only functional but also beautiful. Whether it is a small wooden box or a grand temple, Sao-shachi-tsugi is a testament to the enduring legacy of traditional Japanese carpentry.
The Art of Japanese Joinery
Japanese joinery is renowned for its precision and elegance. It is rooted in a deep understanding of wood and its natural properties. To achieve flawless joinery, craftsmen follow key principles and rely on a specific set of tools.
Japanese joinery has a rich history that dates back centuries. It is a traditional craft that has been passed down from generation to generation, with each new craftsman building upon the knowledge and techniques of their predecessors. The art of Japanese joinery is not simply about connecting two pieces of wood together; it is about creating a harmonious relationship between the wood and the structure it supports.
Key Principles of Japanese Joinery
Japanese joinery is guided by several fundamental principles, including interlocking, balance, and flexibility. Each joint is carefully designed to distribute loads evenly and allow for natural movement and expansion of the wood. This ensures the long-term stability of the structure.
Interlocking is a key principle in Japanese joinery. It involves creating joints that fit together like puzzle pieces, without the need for nails or screws. This not only adds to the aesthetic appeal of the joinery but also enhances its strength and durability. The interlocking joints are meticulously crafted to create a tight and secure fit, ensuring that the structure will withstand the test of time.
Balance is another important principle in Japanese joinery. It involves creating joints that distribute the weight and forces evenly throughout the structure. This not only ensures the stability of the joinery but also enhances its overall strength. By carefully considering the balance of the joints, Japanese craftsmen are able to create structures that are not only functional but also visually pleasing.
Flexibility is a unique aspect of Japanese joinery. Unlike traditional Western joinery, which often relies on rigid connections, Japanese joinery allows for natural movement and expansion of the wood. This is achieved through the use of joints that can flex and adjust to changes in temperature and humidity. By allowing the wood to move naturally, Japanese joinery ensures that the structure remains stable and intact, even in changing environmental conditions.
Tools Used in Japanese Joinery
Japanese carpenters employ a unique set of tools to create their masterpieces. These tools include a variety of saws, chisels, and planes, each specifically designed to achieve precise cuts and smooth surfaces. By using these traditional tools, craftsmen are able to work in harmony with the wood, resulting in joinery of unparalleled quality.
One of the most iconic tools used in Japanese joinery is the pull saw, also known as a "nokogiri." This saw has a thin, flexible blade that allows for precise cuts with minimal effort. The pull motion of the saw also reduces the risk of the blade bending or binding, ensuring clean and accurate cuts every time.
Chisels are another essential tool in Japanese joinery. These chisels, known as "nomi," have a hollow-ground back and a beveled edge, allowing for precise and controlled cutting. Japanese chisels are made from high-quality steel, which holds its edge for longer periods of time, reducing the need for frequent sharpening.
Planes, or "kanna," are used to create smooth and flat surfaces in Japanese joinery. These planes have a wooden body and a sharp blade that is set at a shallow angle. By carefully adjusting the depth and angle of the blade, craftsmen are able to remove thin shavings of wood, resulting in a smooth and even surface.
In addition to these tools, Japanese carpenters also use a variety of other specialized tools, such as marking gauges, mallets, and layout squares. Each tool is meticulously crafted and designed to achieve specific tasks, allowing craftsmen to create joinery of exceptional quality and precision.
The Technique of Sao-shachi-tsugi
When it comes to woodworking, the technique of Sao-shachi-tsugi is truly remarkable. This traditional Japanese method allows craftsmen to create seamless joints with unparalleled accuracy and precision. While it may appear complex at first glance, Sao-shachi-tsugi can actually be broken down into a step-by-step process that ensures the creation of flawless joints.
Let's delve into the fascinating world of Sao-shachi-tsugi and explore the meticulous steps involved in mastering this technique.
Step-by-Step Guide to Sao-shachi-tsugi
1. Preparation: The journey towards a perfect Sao-shachi-tsugi joint begins with careful wood selection. Craftsmen meticulously choose each piece, ensuring that it is straight and free of any defects. This attention to detail ensures that the joint will be strong and durable. Once the wood is selected, the dimensions of the joint are determined, and the wood is marked accordingly. Every mark is made with precision, setting the stage for the intricate cuts to come.
2. Cutting: Armed with precision saws and chisels, the carpenter embarks on the cutting phase. This is where true skill and expertise come into play. Following the marked lines, the carpenter makes precise cuts, ensuring that each one is executed with utmost accuracy. The goal is to create clean and smooth edges that will fit together seamlessly. The carpenter's steady hand and unwavering focus are essential during this critical stage.
3. Interlocking: With the cuts made, it's time to bring the pieces together. The carpenter carefully assembles the wood, ensuring that the interlocking joints fit together like a perfectly crafted puzzle. This requires patience, skill, and a keen eye for detail. Each piece must align perfectly, leaving no room for gaps or imperfections. The satisfaction of seeing the joints come together flawlessly is unparalleled.
Common Mistakes and How to Avoid Them
While Sao-shachi-tsugi demands a high level of skill and precision, there are common mistakes that can be avoided with careful attention to detail. One of the most common errors is improper marking. If the marks are not accurately placed, it can throw off the entire joint, resulting in a less-than-desirable outcome. To avoid this, craftsmen take their time to ensure that every mark is precise and in the right position.
Inaccurate cuts are another pitfall that craftsmen must be wary of. Even the slightest deviation from the marked lines can compromise the joint's integrity. To prevent this, carpenters rely on their steady hands and sharp tools, making each cut with unwavering accuracy.
Insufficient test fitting is yet another mistake that can lead to disappointing results. Before final assembly, it is crucial to test fit the pieces together. This allows craftsmen to identify any discrepancies or areas that need adjustment. By taking the time to double-check measurements and test fit the pieces, these mistakes can be minimized or avoided altogether.
As you can see, Sao-shachi-tsugi is not just a technique; it is an art form that demands patience, skill, and unwavering attention to detail. Craftsmen who master this technique are truly able to create woodworking masterpieces that stand the test of time. So, the next time you admire a beautifully crafted joint, take a moment to appreciate the meticulous process that went into its creation.
The Role of Sao-shachi-tsugi in Japanese Architecture
Sao-shachi-tsugi has played a significant role in shaping traditional Japanese architecture, and its influence can still be seen in modern structures.
Influence on Traditional Japanese Buildings
Traditional Japanese buildings, such as temples, tea houses, and shrines, have long been revered for their beauty and craftsmanship. Sao-shachi-tsugi is often used in these structures, showcasing the skill and expertise of Japanese carpenters. The joints not only provide structural integrity but also add a unique aesthetic appeal.
Sao-shachi-tsugi in Modern Architecture
While modern construction methods have introduced alternative techniques and materials, Sao-shachi-tsugi continues to be used in contemporary architecture. Architects and designers recognize the value of this traditional joinery method, not only for its durability but also for the sense of authenticity it brings to a space.
Preserving the Tradition of Sao-shachi-tsugi
As with many traditional crafts, the preservation of Sao-shachi-tsugi relies on a commitment to craftsmanship and a recognition of its importance in maintaining cultural heritage.
The Importance of Craftsmanship
Craftsmanship lies at the heart of Sao-shachi-tsugi. The intricate joinery cannot be replicated through mass production or shortcuts. It requires dedicated craftsmen who possess a deep understanding of wood, tools, and techniques. By valuing craftsmanship, we ensure that the art of Sao-shachi-tsugi continues to be passed down to future generations.
Future of Sao-shachi-tsugi in Japan and Beyond
While the tradition of Sao-shachi-tsugi remains rooted in Japan, its influence has spread worldwide. As more architects and craftsmen recognize the value of this unique joinery technique, Sao-shachi-tsugi is gaining popularity beyond Japanese borders. By embracing and preserving this tradition, we can ensure that the art of Sao-shachi-tsugi continues to thrive for years to come.
In conclusion, Sao-shachi-tsugi is more than just a joinery technique; it is a reflection of Japanese craftsmanship, philosophy, and culture. Through centuries of refinement, this traditional method has sculpted much of Japan's architectural landscape. By understanding and appreciating Sao-shachi-tsugi, we can gain a deeper appreciation for the artistry and skill involved in Japanese carpentry, and ensure that this rich tradition continues to inspire future generations of craftsmen around the world.
Inspired by the timeless beauty and precision of Sao-shachi-tsugi joinery, Quagga Designs brings the same dedication to craftsmanship and sustainability to your home with our easy-to-assemble, MADE IN CANADA bed frames. Our No-Fuss Plus and Tic-Tac-Toe beds require no hardware, embodying the spirit of traditional techniques while offering modern convenience—assembly takes less than 10 minutes, often outpacing the time it takes to unbox. The No-Fuss Plus bed's innovative design expands to accommodate your changing needs, from single to double, and queen to king sizes. Similarly, the Accordion bed caters to a range of mattress sizes including single xl, double xl, queen, and king. Committed to environmental responsibility, we use all-natural soy-based glue from Columbia Forest Products and source FSC Certified Maple wood from Quebec, Canada. The Mahogany for our No-Fuss Plus bed, also FSC Certified, is a tone wood esteemed by renowned guitar builders like Fender, adding a touch of musical heritage to its rich aesthetics. With no formaldehyde, Carb P2 compliance, and a focus on reducing landfill impact, Quagga bed frames are a testament to our dedication to the environment. Customizable to your taste and designed to support increased weight capacity, our bed frames are not only versatile but also support local economies. We proudly ship throughout Canada and the continental United States, partner with charitable organizations, and offer a 1-year warranty alongside a 100-night sleep trial. Experience the fusion of Japanese-inspired joinery and Canadian craftsmanship with Quagga Designs, where every bed frame tells a story of beauty, durability, and conscientious living. Check out our products and join us in preserving a legacy of quality and sustainability.