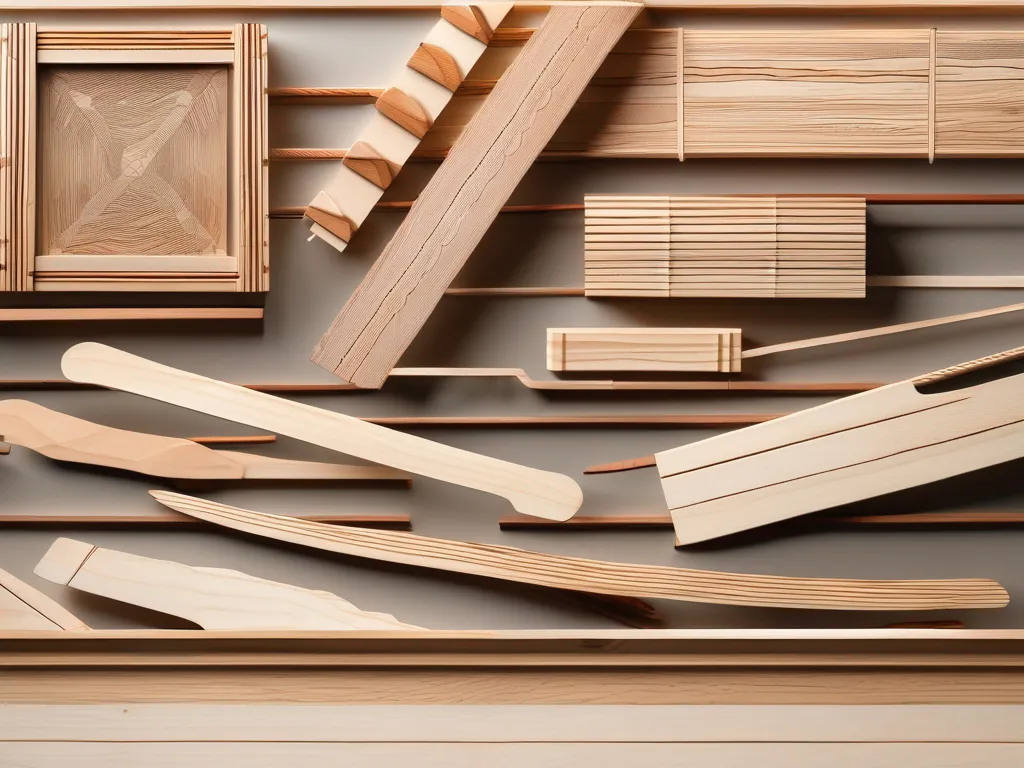
Japanese joinery is renowned for its precision and craftsmanship. One particular joinery technique that exemplifies this mastery is Shihou-kama-tsugi. In this article, we will delve into the intricacies of Shihou-kama-tsugi, exploring its history, key features, and its role in Japanese architecture. We will also take a closer look at the art and science of Japanese joinery, as well as the process of creating a Shihou-kama-tsugi joint. Lastly, we will discuss the future of Shihou-kama-tsugi and Japanese joinery, including innovations and the importance of preserving this ancient craft.
Understanding the Basics of Shihou-kama-tsugi
To truly appreciate Shihou-kama-tsugi, it is essential to understand its origins and its significance in Japanese culture. This joinery method has been prevalent for centuries, with its roots in traditional Japanese carpentry. Shihou-kama-tsugi involves connecting wooden elements by interlocking their corners, creating a tight and durable joint that requires no nails or adhesives.
The History and Evolution of Shihou-kama-tsugi
The origins of Shihou-kama-tsugi can be traced back to ancient Japan, where it was first used in the construction of shrines and temples. The craftsmen of that time recognized the need for a joint that could withstand the test of time and natural forces. They developed Shihou-kama-tsugi as a solution, combining their knowledge of wood properties and structural integrity.
As time went on, Shihou-kama-tsugi evolved alongside the changing architectural styles and preferences. It became a staple in traditional Japanese architecture, not only for its functionality but also for its aesthetic appeal. The intricate interlocking corners became a symbol of craftsmanship and attention to detail.
During the Edo period in Japan, Shihou-kama-tsugi gained even more popularity. With the rise of the tea ceremony culture, the demand for beautifully crafted tea houses increased. Shihou-kama-tsugi was often used in the construction of these tea houses, showcasing the skill and artistry of the carpenters.
Key Features of Shihou-kama-tsugi
One of the distinguishing features of Shihou-kama-tsugi is its meticulous attention to detail. The craftsmen who practice this joinery method spend countless hours ensuring that each corner fits perfectly, creating a seamless connection between the wooden elements. This attention to detail not only enhances the structural integrity of the joint but also adds to the overall beauty of the finished piece.
Another key feature of Shihou-kama-tsugi is its ability to withstand heavy loads. The interlocking corners create a strong and stable connection, making it ideal for load-bearing structures such as beams and columns. The self-locking mechanism of the joints further enhances their strength, ensuring that the wooden elements stay securely in place even under pressure.
Furthermore, Shihou-kama-tsugi is known for its longevity. The tight fit of the joints, combined with the natural properties of the wood, allows the joint to expand and contract with changes in temperature and humidity. This flexibility helps to prevent the joint from loosening or cracking over time, ensuring that the structure remains sturdy and durable for years to come.
In conclusion, Shihou-kama-tsugi is not just a joinery method; it is a testament to the rich history and craftsmanship of traditional Japanese carpentry. Its origins in ancient Japan, its evolution alongside architectural styles, and its key features of attention to detail, load-bearing capability, and longevity all contribute to its significance in Japanese culture. Whether used in the construction of shrines, temples, tea houses, or other structures, Shihou-kama-tsugi continues to be admired and respected for its beauty and functionality.
The Art and Science of Japanese Joinery
Japanese joinery is a unique fusion of art and science. It encompasses a set of principles and techniques that have been refined over centuries. Understanding these principles is crucial for mastering the art of Japanese joinery.
Japanese joinery is deeply rooted in the country's rich cultural heritage. It is not just a practical skill, but also a form of artistic expression. The craftsmanship involved in creating intricate joints is highly regarded and admired.
Principles of Japanese Joinery
At the core of Japanese joinery lies a deep respect for the natural properties of wood. The principles emphasize the use of precise measurements, balance, and a harmonious relationship between the materials and the environment. Each joint is meticulously crafted to achieve both functionality and aesthetic appeal.
Japanese joinery takes into account the unique characteristics of different types of wood. The carpenters carefully select the appropriate wood species for each joint, considering factors such as strength, durability, and grain pattern. This attention to detail ensures that the joints will withstand the test of time.
The principles of Japanese joinery also emphasize the importance of balance and symmetry. The joints are designed to distribute the weight evenly, creating stability and ensuring the longevity of the structure. The carpenters carefully calculate the angles and dimensions of each joint to achieve perfect balance.
Tools and Techniques in Japanese Joinery
Japanese carpenters rely on a variety of specialized tools to execute their craft. From hand planes and chisels to saws and hammers, each tool is designed to cut and shape wood with utmost precision. Traditional techniques, such as meticulous hand-cutting and delicate carving, lend themselves to the precise joinery found in Shihou-kama-tsugi.
The tools used in Japanese joinery are not just ordinary tools; they are works of art in themselves. Many of these tools are handcrafted by skilled artisans who have dedicated their lives to perfecting their craft. The blades of the chisels and planes are meticulously sharpened to ensure clean and precise cuts. The handles of the tools are often made from beautiful and durable materials, such as rosewood or ebony, adding to their aesthetic appeal.
Japanese joinery techniques are passed down from generation to generation, with master craftsmen teaching their apprentices the secrets of the trade. The apprentices spend years honing their skills, learning the intricacies of each joint and perfecting their technique. This tradition of mentorship ensures that the art of Japanese joinery continues to thrive and evolve.
Japanese joinery is not just about creating functional structures; it is about creating works of art that stand the test of time. The attention to detail, precision, and craftsmanship involved in Japanese joinery make it a truly remarkable and awe-inspiring art form.
The Process of Creating a Shihou-kama-tsugi Joint
Creating a Shihou-kama-tsugi joint requires meticulous planning and execution. This step-by-step guide will walk you through the process, ensuring that you achieve a seamless and secure connection between the wooden elements.
A Shihou-kama-tsugi joint is a traditional Japanese woodworking technique that involves creating a four-way interlocking joint. This joint is commonly used in the construction of furniture, cabinets, and other wooden structures. It not only provides structural stability but also adds an aesthetic appeal to the finished piece.
Step-by-Step Guide to Shihou-kama-tsugi
- Prepare the wood: Start by selecting high-quality timber and ensuring that it is properly dried and seasoned. The wood should be free from knots, cracks, and other defects that could weaken the joint.
- Measure and mark: Accurate measurements are crucial for a successful joint. Use a square and marking tools to determine the precise locations for the cuts. Take your time to ensure that the measurements are precise, as even a slight deviation can affect the fit of the joint.
- Make the cuts: Carefully use saws, chisels, and other cutting tools to create the necessary grooves and notches in the wooden elements. The cuts should be clean and precise, following the marked lines. Take care not to remove too much material, as it can weaken the joint.
- Test the fit: Trial and error is a vital part of the process. Test the fit of the pieces and make any necessary adjustments until the joint fits snugly, with no gaps. This may involve fine-tuning the cuts or using a chisel to remove any excess material.
- Assemble and secure: Once you are satisfied with the fit, assemble the joint by carefully sliding the interlocking pieces together. Apply minimal pressure to the joined pieces, causing the joint to self-lock. If required, use wooden pegs or wedges for added stability. These can be inserted through pre-drilled holes to further secure the joint.
Creating a Shihou-kama-tsugi joint requires a combination of skill, patience, and attention to detail. It is a technique that has been perfected over centuries by Japanese craftsmen, and mastering it can take time and practice.
Common Mistakes and How to Avoid Them
While creating a Shihou-kama-tsugi joint may seem straightforward, there are common pitfalls that beginners often encounter. One of the main mistakes is rushing the process or neglecting accurate measurements. Patience and precision are key to achieving a flawless joint.
Another common mistake is not properly preparing the wood. Using low-quality or improperly dried timber can result in weak joints that are prone to splitting or warping over time. It is essential to select the right type of wood and ensure that it is properly seasoned before starting the joint-making process.
Additionally, not testing the fit thoroughly can lead to problems later on. It is important to take the time to test the joint at each stage of the process and make any necessary adjustments. This will ensure that the final joint is strong, secure, and aesthetically pleasing.
Lastly, it is crucial to use the right tools and techniques for creating a Shihou-kama-tsugi joint. Using dull or improper tools can result in rough cuts and imprecise joints. Investing in high-quality woodworking tools and learning proper cutting techniques will greatly improve the quality of your joints.
By avoiding these common mistakes and following the step-by-step guide, you can create beautiful and durable Shihou-kama-tsugi joints that will enhance your woodworking projects.
The Role of Shihou-kama-tsugi in Japanese Architecture
Shihou-kama-tsugi has played a vital role in traditional Japanese architecture, contributing to the strength, durability, and aesthetic appeal of structures. Understanding its significance provides insight into the architectural heritage of Japan.
Shihou-kama-tsugi in Traditional Japanese Buildings
Traditional Japanese buildings, such as temples, tea houses, and pagodas, often feature complex joinery systems, with Shihou-kama-tsugi as a prominent component. These joints not only provide structural stability but also showcase the craftsmanship and artistic sensibilities of the builders.
Modern Applications of Shihou-kama-tsugi
While Shihou-kama-tsugi originated in traditional contexts, its influence can still be seen in modern architecture. Contemporary designers and architects draw inspiration from Japanese joinery techniques, incorporating them into innovative and sustainable designs.
The Future of Shihou-kama-tsugi and Japanese Joinery
As the world becomes increasingly fast-paced and technology-driven, preserving traditional crafts such as Shihou-kama-tsugi is of utmost importance. However, this does not mean that Japanese joinery is stagnant. There are ongoing innovations and developments that seek to push the boundaries of this ancient craft.
Innovations and Developments in Japanese Joinery
Advancements in materials, tools, and techniques are expanding the possibilities of Japanese joinery. Hybrid joinery systems, combining traditional methods with modern technology, offer unique opportunities for experimentation and creativity.
Preserving the Craft of Shihou-kama-tsugi
Efforts to preserve the craft of Shihou-kama-tsugi and Japanese joinery are essential to ensure that future generations can experience the beauty and functionality of these techniques. Apprenticeships, master-apprentice relationships, and educational programs play a crucial role in passing down the knowledge and skills required for this ancient craft to thrive.
In conclusion, Shihou-kama-tsugi is a testament to the skill and precision of Japanese joinery. Its rich history, key features, and intricate connection process make it a captivating subject. Whether used in traditional or modern contexts, Shihou-kama-tsugi continues to inspire and showcase the enduring legacy of Japanese craftsmanship.
Inspired by the timeless art of Shihou-kama-tsugi and the unparalleled craftsmanship of Japanese joinery, Quagga Designs brings the same ethos of beauty, functionality, and sustainability to your bedroom. Our easy-to-assemble, MADE IN CANADA bed frames, such as the innovative No-Fuss Plus and the versatile Tic-Tac-Toe beds, embody the spirit of traditional joinery with a modern twist. With no hardware required and an assembly time of less than 10 minutes, you can transform your space with ease. Our expandable No-Fuss Plus bed frame adapts from single to double and queen to king sizes, while the Accordion bed accommodates a range of mattress sizes, ensuring that you won't need to replace your bed frame when upgrading your mattress. Crafted from FSC Certified Maple wood sourced in Quebec and Mahogany with a rich tone revered by guitar builders, our bed frames are not only environmentally friendly but also a testament to Canadian craftsmanship. By choosing Quagga Designs, you support our local economy, benefit from a 1-year warranty, and contribute to charitable causes. Experience the comfort of our bed frames with a 100-night sleep trial and enjoy swift shipping across Canada and the continental United States. Check out our products and join us in preserving the legacy of skilled joinery while embracing innovation and sustainability.