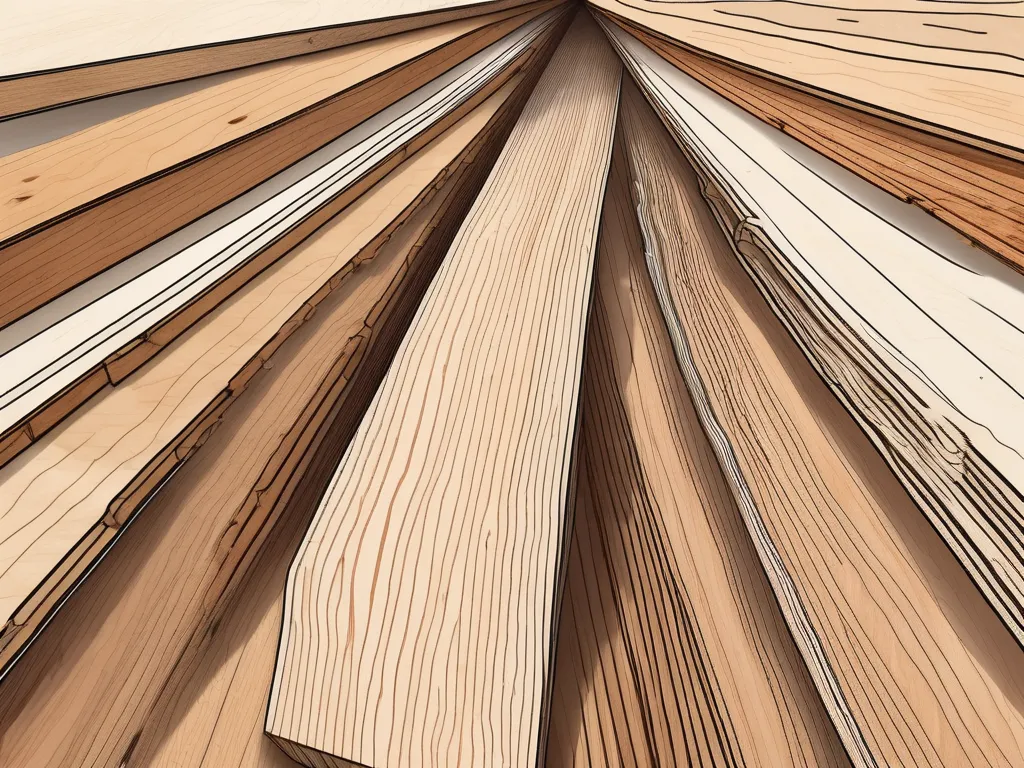
A common misconception in woodworking is that hardwood is inherently stronger than plywood. While hardwood does have many desirable qualities, plywood actually surpasses it in terms of strength and stability. Understanding the composition, manufacturing process, and properties of plywood and hardwood can shed light on why plywood trumps hardwood in strength. Foundation for a good sleep is also a natural wood bed frame such the Quagga Designs bed frames.
Understanding the Composition of Plywood
Plywood is a composite material made up of several layers, or plies, of wood veneer. Each layer is typically oriented perpendicular to the adjacent layers, resulting in a cross-grain construction. This arrangement creates a strong and stable panel that resists warping and cracking.
But what exactly makes plywood such a remarkable material? Let's delve deeper into its layers and the glue that holds them together.
Layers and Glue: The Strength of Plywood
The number of layers in plywood can vary, but the typical construction consists of three or more layers. These layers are bonded together with high-quality adhesives, such as phenol formaldehyde, which provide excellent strength and durability. The adhesive acts as the backbone of plywood, ensuring that the layers remain firmly intact.
One might wonder, why is the orientation of the layers so crucial? Well, the cross-grain configuration plays a significant role in plywood's strength. When the layers are arranged perpendicular to each other, it creates a balanced structure that distributes the load evenly. This design prevents the panel from warping or cracking under pressure, making plywood a reliable choice for various applications.
Moreover, the adhesive bond between the layers further enhances the strength of plywood. The high-quality glue not only holds the layers together but also increases the overall structural integrity. This adhesive bond allows plywood to withstand heavy loads and resist the effects of moisture and temperature changes.
The Manufacturing Process of Plywood
Plywood is not just a simple assembly of wood veneers; it undergoes a meticulous manufacturing process to ensure its exceptional quality. Let's take a closer look at how plywood is made.
The journey of plywood begins with logs, which are carefully selected for their quality and characteristics. These logs are then peeled into thin veneers using a rotary cutting process. The veneers are meticulously dried to remove any moisture, ensuring stability and preventing future warping.
Once the veneers are ready, they are sorted based on their quality. This step ensures that only the finest veneers are used in the construction of plywood, guaranteeing a superior end product.
Next comes the critical step of layering the veneers. The layers are arranged with alternating grain directions, which further enhances the strength and stability of the final product. The adhesive, such as phenol formaldehyde, is carefully applied between each layer, ensuring a strong bond.
After the layers are assembled, the panel undergoes a pressing process under high pressure and heat. This step is crucial as it activates the adhesive and creates a strong bond between the layers. The high pressure ensures that the layers are tightly compressed, resulting in a solid and durable plywood panel.
It is worth noting that the manufacturing process of plywood eliminates many defects found in solid wood. Knots, cracks, and other imperfections are minimized, resulting in a more consistent and uniform material. This consistency makes plywood an ideal choice for applications where strength and uniformity are essential.
In conclusion, plywood's composition and manufacturing process contribute to its exceptional strength, stability, and durability. By understanding the layers, glue, and manufacturing techniques involved, we can truly appreciate the remarkable qualities of this versatile material.
The Properties of Hardwood
Hardwood, derived from deciduous trees, is highly regarded for its natural beauty, durability, and longevity. Its unique cell structure and high density contribute to its strength and resistance to wear and tear.
When it comes to hardwood, its natural structure plays a crucial role in determining its exceptional properties. Hardwood consists of cells that are tightly packed and interlocked, forming a dense and solid material. This feature enhances the wood's strength, allowing it to withstand heavy loads and resist deformation. The presence of dense fibers and natural resins in hardwood further enhances its durability, making it a preferred choice for various applications.
One fascinating aspect of hardwood is its ability to adapt to different environments. The unique cell structure of hardwood allows it to expand and contract with changes in temperature and humidity, making it highly stable and resistant to warping or twisting. This characteristic is particularly important in areas with fluctuating climate conditions, as it ensures that the hardwood maintains its structural integrity over time.
The Natural Structure of Hardwood
Hardwood consists of cells that are tightly packed and interlocked. This feature enhances the wood's strength, allowing it to withstand heavy loads and resist deformation. The presence of dense fibers and natural resins in hardwood further enhances its durability.
Furthermore, the natural structure of hardwood contributes to its stunning aesthetic appeal. The interlocking cells create unique grain patterns that vary from species to species, giving each piece of hardwood its own distinct character. From the elegant and straight grain of oak to the rich and swirling patterns of mahogany, hardwood offers a wide range of visual options that can complement any interior design style.
In addition to its visual appeal, the natural structure of hardwood also affects its workability. The tightly packed cells make it easier to shape and carve, allowing craftsmen to create intricate designs and details. This workability is particularly advantageous in the production of fine furniture, where the ability to achieve precise cuts and joinery is essential.
Factors Affecting Hardwood Strength
While hardwood is naturally strong, several factors can affect its overall strength. The species of the wood, its grain pattern, and the presence of knots or defects can impact its performance. Different hardwood species have varying levels of hardness and density, which directly influence their strength and durability. For example, woods like hickory and maple are known for their exceptional hardness, making them suitable for high-traffic areas or heavy-duty applications.
Moreover, the grain pattern of hardwood can also influence its strength. Woods with straight grain patterns, such as ash or birch, tend to be stronger and more resistant to splitting. On the other hand, woods with irregular or interlocking grain patterns, like walnut or cherry, may have slightly lower strength but offer unique visual appeal.
Additionally, the presence of knots or defects in hardwood can weaken its overall strength. Knots are areas where branches have grown and are typically denser and harder than the surrounding wood. While small knots may not significantly affect the strength of hardwood, larger or more numerous knots can compromise its structural integrity.
Lastly, changes in moisture content can cause hardwood to expand or shrink, potentially compromising its strength and stability. It is important to properly acclimate and install hardwood flooring or furniture to ensure that it can adjust to the surrounding environment without causing any issues.
In conclusion, hardwood is a remarkable material with a unique cell structure and high density that contribute to its strength and durability. Its natural beauty, combined with its ability to withstand wear and tear, make it an excellent choice for a wide range of applications. Understanding the natural structure and factors affecting hardwood strength can help in selecting the right type of hardwood for specific projects and ensure its long-lasting performance.
Comparing Plywood and Hardwood Strength
When evaluating the strength of plywood and hardwood, it is important to consider various factors.
Strength is a crucial aspect to consider when choosing between plywood and hardwood for different applications. Plywood, with its layered construction and perpendicular grain orientation, distributes weight evenly across the panel, making it highly effective in load-bearing applications such as flooring and roofing. The layers of wood are bonded together with strong adhesives, creating a sturdy and durable material. This structural integrity allows plywood to withstand heavy loads without sagging or buckling, making it a popular choice for construction projects that require high load-bearing capabilities.
On the other hand, while hardwood is known for its strength, it may have variations in grain direction and consistency that can affect its load-bearing capacity. Hardwood boards are typically cut from a single piece of wood, which means that the grain may not always run in the desired direction for optimal strength. This can result in weaker areas within the wood, making it less suitable for certain load-bearing applications.
Resistance to Warping and Shrinkage
Plywood's cross-grain construction and adhesive bond significantly reduce the risk of warping and shrinkage compared to solid hardwood. The alternating layers of wood in plywood help counteract the natural tendency of wood to expand and contract with changes in temperature and humidity. This results in a more stable and dimensionally reliable material, making plywood an excellent choice for applications where dimensional stability is crucial.
Hardwood, on the other hand, is more prone to warping and shrinkage due to its solid construction. As a natural material, hardwood reacts to changes in moisture content, causing it to expand and contract. This can lead to warping, cupping, and gaps between boards. While hardwood can be treated and sealed to minimize these effects, it still requires regular maintenance to ensure its long-term stability.
Furthermore, plywood's adhesive bond between layers adds an extra layer of protection against warping and shrinkage. The adhesive helps to hold the layers together, preventing them from separating or warping under different environmental conditions. This makes plywood a reliable choice for applications where dimensional stability is critical, such as in high-humidity environments or areas with significant temperature fluctuations.
Practical Applications of Plywood vs Hardwood
Both plywood and hardwood find numerous applications across various industries.
Plywood in Construction
Plywood's strength, versatility, and cost-effectiveness make it a popular choice in construction. It is used for sheathing, subfloors, support beams, and formwork. Its structural integrity and resistance to moisture make it ideal for outdoor projects as well.
Hardwood in Furniture Making
Hardwood's aesthetic appeal, durability, and ability to be shaped and carved make it a preferred material for furniture making. It is often used to create high-quality pieces that stand the test of time.
Cost and Sustainability Considerations
When choosing between plywood and hardwood, several factors should be considered, including cost and sustainability.
Evaluating the Cost-Effectiveness
Plywood is generally more cost-effective than hardwood due to its manufacturing process and availability. The ability to use thinner layers of wood and the efficient use of natural resources help keep the cost of plywood lower. Hardwood, on the other hand, tends to be more expensive due to its sourcing, processing, and quality.
Environmental Impact of Plywood and Hardwood Production
Plywood production involves the efficient use of wood resources and can be considered a sustainable option. Many plywood manufacturers also adhere to responsible forestry practices and use adhesives that are free from harmful substances. Hardwood production, however, can have a higher ecological impact as it often requires the harvesting of entire trees. Sustainable forest management and responsible sourcing can help mitigate these concerns.
Conclusion
While hardwood possesses its own unique qualities and appeal, plywood emerges as the superior choice when it comes to strength and stability. The composition, manufacturing process, and properties of plywood give it an edge over hardwood in load-bearing capabilities, resistance to warping, and cost-effectiveness. Understanding these factors helps inform the decision-making process when choosing between plywood and hardwood for various applications.
Embrace the strength and stability of plywood with Quagga Designs' innovative bed frames. Our easy-to-assemble, MADE IN CANADA bed frames, such as the No-Fuss Plus and the Tic-Tac-Toe, showcase the durability and versatility of plywood, taking less than 10 minutes to set up. With the No-Fuss Plus's expandable design and the Accordion bed's adaptability to various mattress sizes, you'll never need to replace your bed frame again. Crafted with eco-friendly, soy-based glue and FSC Certified Maple and Mahogany, our bed frames are not only environmentally conscious but also free of formaldehyde. Plus, they offer the flexibility to personalize with your choice of stain or paint. Proudly supporting our local economy and partnering with charitable organizations, Quagga Designs is committed to excellence, offering a 5-year warranty and a 100-night sleep trial. Experience the most environmentally clean and customizable bed frames on the market. Check out our products and join the Quagga family today.